PRE-ENGINEERED BUILDING – ADVANTAGES AND IMPORTANT NOTES
Pre-engineered building, also known as Pre-engineered steel buildings (PEBs). Are a growing trend in the construction industry. They offer numerous benefits in terms of cost and time efficiency, making them a preferred choice for many developers and investors. In this article, we will delve into the advantages and important considerations of pre-engineered building
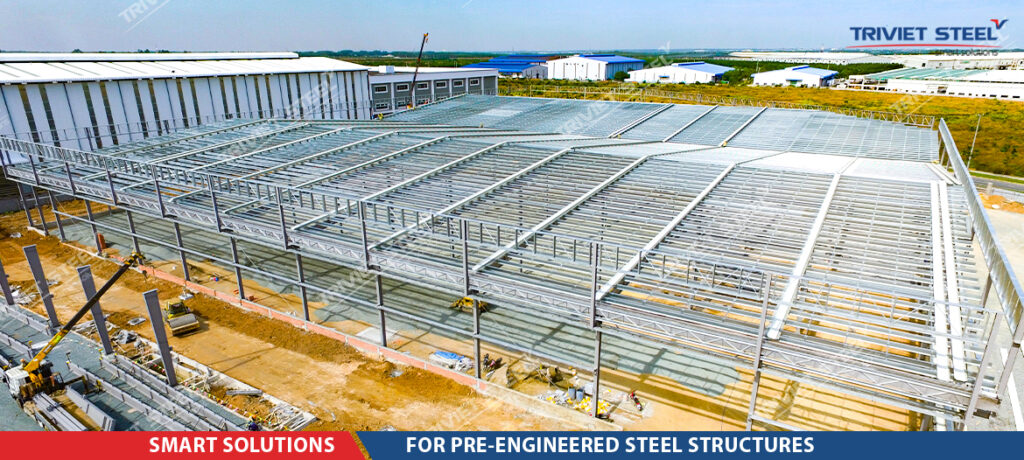
1. Overview of Pre-Engineered Building
Pre-engineered building are structures primarily made of steel. The steel components that form the main structure of the building are manufactured in factories and then transported to the construction site, where they are assembled according to predetermined design drawings.
There are three common types of pre-engineered building:
- Industrial: such as warehouses, factories, and storage facilities.
- Manufacturing: including production plants and manufacturing towers.
- Commercial: encompassing supermarkets, shopping centers, and showrooms.
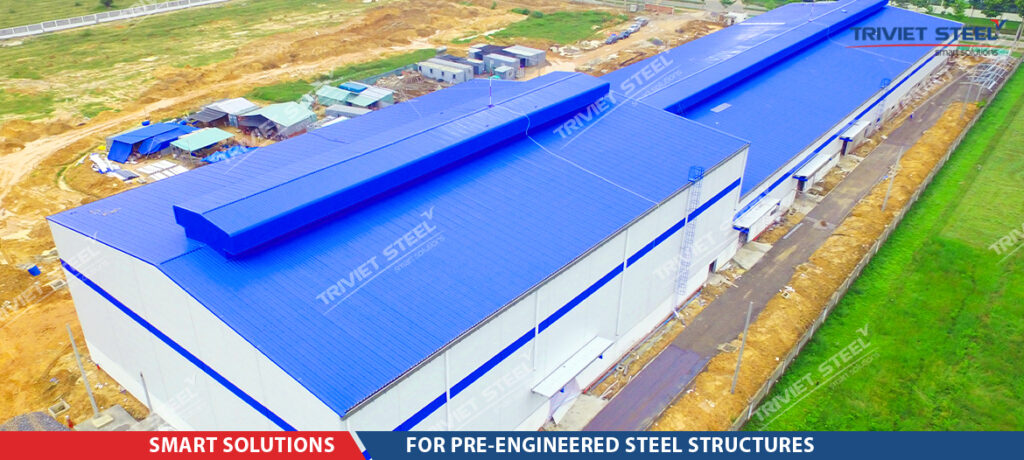
2. Advantages of Pre-Engineered Building in Construction
Pre-engineered building offer several notable advantages:
- Streamlined and Cost-Effective: Designing and fabricating our pre-engineered steel components in controlled factory environments provide several cost-saving advantages. We then transport these pre-fabricated components to the construction site, minimizing material waste and significantly reducing construction time.. Compared to traditional reinforced concrete structures, this innovative approach can result in approximately 30% cost savings, making it a highly attractive option for budget-conscious projects.
- Exceptional Strength and Durability: The steel framework employed in our pre-engineered structures significantly minimizes the overall weight of the building while simultaneously enhancing its load-bearing capacity. This allows the building to withstand heavy loads, ensuring long-term structural integrity and exceptional durability. The inherent malleability and strength of steel further contribute to the robust nature of the building, guaranteeing its performance for generations to come.
- Faster Construction Timelines: Thanks to pre-fabrication, all structural steel components are designed, manufactured, and quality-inspected in the factory prior to being transported to the construction site for quick and efficient installation. This streamlined process significantly reduces construction time compared to traditional methods, enabling faster project completion and earlier occupancy. Additionally, the pre-fabricated components offer complete transparency and assurance, allowing developers to directly assess the product quality before installation.
- Flexibility for Expansion and Upgrading: A key advantage of our pre-engineered steel structures is their modularity and flexibility. The steel components are connected using bolted connections, allowing for easy disassembly and reassembly. This inherent flexibility proves highly beneficial for future expansion or modification of the building, enabling developers to adapt the space to evolving needs without significant structural changes or complex reconstruction processes.
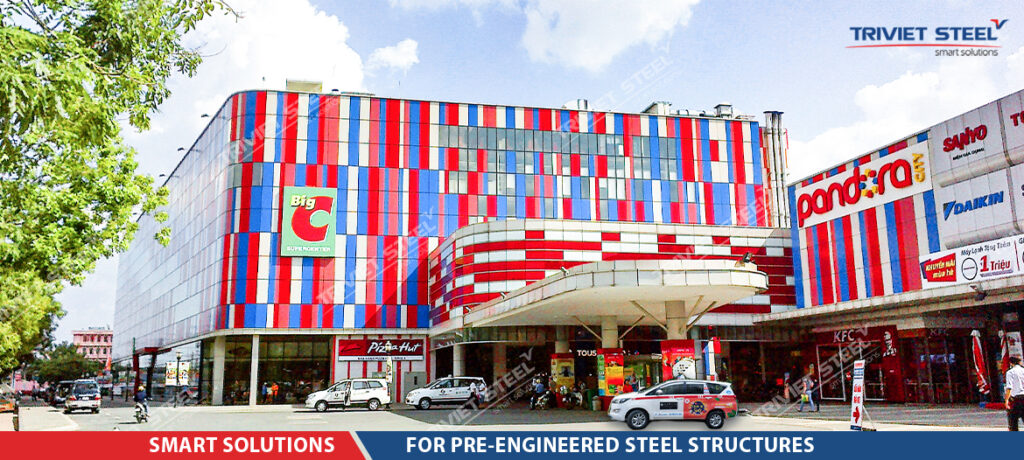
3. Important Notes for Pre-Engineered Building
While pre-engineered building offer numerous advantages, there are a few important notes to keep in mind:
1. Limitations in Architecture and Interior Design:
Some people believe that PEBs lack aesthetic appeal and are not flexible enough to reflect the owner’s personality. With pre-existing structures and limitations in design, creating a unique and personalized living space can become challenging.
2. Compatibility with the Surrounding Environment:
We often construct pre-engineered building in controlled environments. When we relocate them to different environments, such as uneven terrain or regions with harsh weather conditions, they may face difficulties in terms of compatibility and durability. This is especially true in areas prone to flooding, earthquakes, or severe storms.
3. High Maintenance Costs:
PEBs require regular maintenance to ensure quality and safety. The maintenance costs are typically higher compared to traditional construction methods.
4. Difficult Repairs:
In the event of a malfunction, PEBs are more challenging to repair compared to traditional construction methods. Since the structure of a pre-engineered building is assembled from prefabricated components, damaged components need to be dismantled and replaced. This leads to increased costs and time consumption.
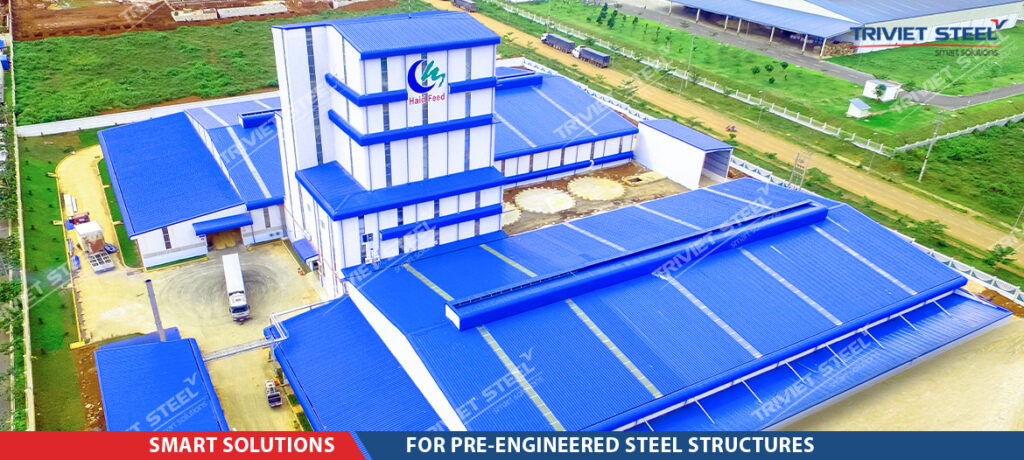
4. Tri Viet Steel – Smart Solution for Pre-Engineered Steel Buildings
Tri Viet Steel is a leading entity in the pre-engineered steel building construction field in Vietnam. With 19 years of experience, Tri Viet Steel has successfully built thousands of pre-engineered steel structures across the country, ranging from residential homes, workshops, warehouses to public, commercial, and industrial projects.
Tri Viet Steel continually strives to provide customers with intelligent, high-quality, and competitively priced solutions in pre-engineered steel construction. With an experienced team of engineers and architects, Tri Viet Steel can meet a wide range of customer needs, from simple requirements to the most complex ones.
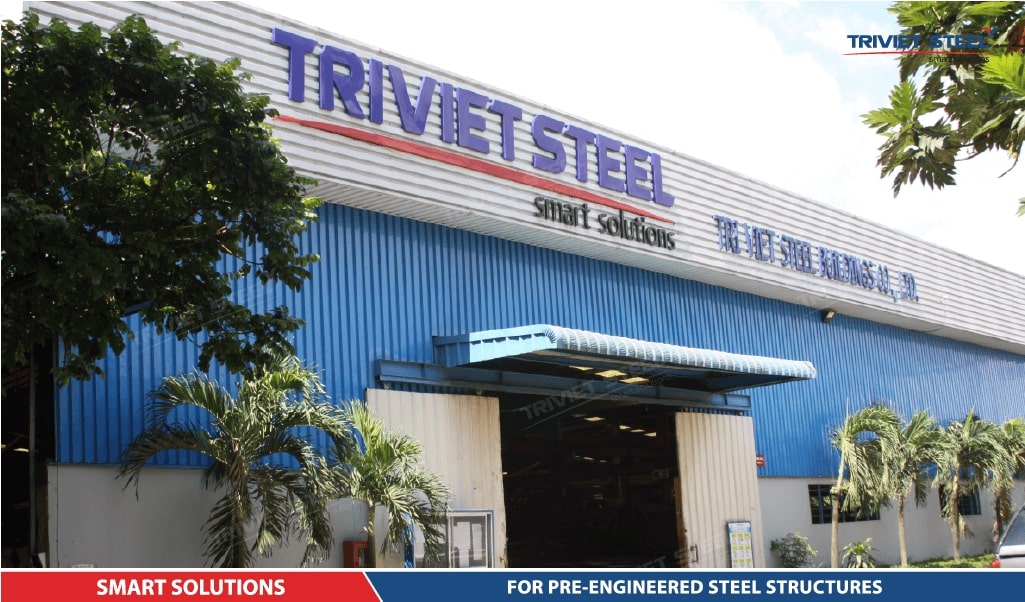